An electronics company in the United States was facing high aluminum corrosion rates and treatment costs in their process cooling water systems due to the previous water treatment program. The previous program resulted in high conductivity and high pH, which no longer met the specifications of 50 microsiemens (µS) and a pH of 6.5 to 7.5. Low conductivity is required for process cooling water tooling applications, and the pH range is required to minimize aluminum corrosion rates. If this problem was left untreated, then the closed loop system components would require repeated replacement. As an example, this facility experienced ammonia stress-related cracking and the failure of brass components along with elevated general corrosion, especially on aluminum.
In an effort to improve efficiency and reduce costs, the electronics production facility recognized that a new treatment program should be considered. In response, Kurita proposed patented film-forming substance (FFS) Cetamine, which would meet their conductivity system requirements while eliminating the need for close pH monitoring due to this technology’s corrosion protection mechanism.
Before starting the treatment program, Kurita established a framework for the customer and a plan of action. Corrosion coupons and other analysis were done with their internal analytical and technical teams. Kurita also showcased a risk mitigation plan based on the facility’s needs. Kurita then proceeded to flush the closed loop system, isolate any blowdown that had been previously necessary to control high conductivity levels, add Kurita’s Cetamine, and evaluate the results.
In previous applications, Cetamine for boilers, cooling towers, and closed loops have been proven to extend equipment life and improve plant productivity by creating a continuous barrier, effectively inhibiting corrosion on all system metallurgy and components without affecting heat transfer.
When initiating a film-forming substances to a system, foaming can be a concern. To mitigate this challenge, Kurita also fed a defoamer. Neither Cetamine nor the defoamer contribute significantly to conductivity. Cetamine treatment in process cooling water systems is a single formulation program that protects the system, replacing the need for most other chemicals. It limits the number of deliveries of other chemicals while lowering the necessary dosage for the system, ultimately reducing overall treatment costs.
Once the new closed loop program was started, the facility observed excellent corrosion protection on their assets and, over the next thirty days, saw exceptional copper, brass, and aluminum corrosion rates.
Many systems require conductivity as low as 50 µS. Kurita was able to meet and exceed this requirement with a fully treated operational conductivity of 12 µS. In addition to this, Kurita maintained a pH between 6.5 and 7.5 with the Cetamine FFS residual between one and three. This also lowered chemical costs, deliveries, and water usage. In total, the facility will save $60,000 annually with Kurita’s Cetamine program.
Originally, the Kurita Cetamine trial was meant to last 90 days, but the facility decided to accelerate the trial to 30 days and then do a mass implementation. All process cooling water systems at this facility are now running on Cetamine. Six other facilities under the same manufacturer are considering implementation of the Cetamine technology now following the positive full-trial results at this location. This semiconductor manufacturer continues to partner with Kurita valuing the new technologies in both equipment and chemistries proven to provide economical and sustainable treatment solutions.
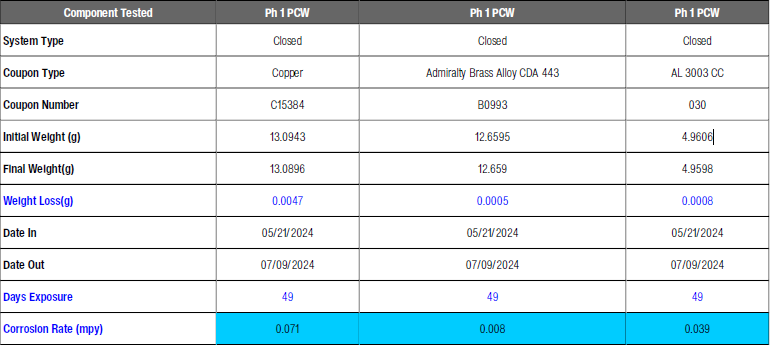
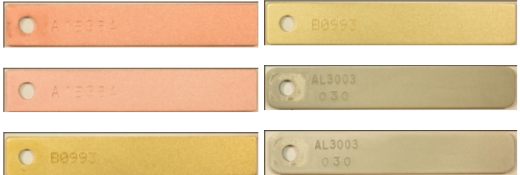