A food ingredients production facility had a chronic issue with process leaks in their heat exchangers at their gelatin processing unit. This resulted in product being sent back to the boiler via the condensate. The gelatin is high viscosity which regularly wore out the seals of the heat exchangers. The gelatin, containing hard water, also caused foaming, and eventually significant scale was formed in the water tube boilers. The issue was compounded by a recent change in personnel in the boiler room as their long-term operator was off work for nearly a year after shoulder surgery. The inexperienced replacement operator missed a problem with the pre-treatment system. The result was prolonged periods of time with condensate contamination and over-cycled boilers due to the high conductivity of the contamination.
After the boiler inspection in July of 2019, the plant wanted to pursue an acid cleaning of the boilers. However, due to the high cost and dangers inherent in acid cleaning, Kurita America's local representative presented another solution to the customer — to try and clean the boilers while online and reevaluate the boiler water side after the next inspection. When the DReeM Polymer products became available later that year, it was discussed to change to this technology from the current all polymer treatment. Our customer was impressed with the supporting data from Japan and Europe, so their facility began the process of getting Kurita's DReeM products approved to use in their system. Being a food and pharmaceutical ingredient producer, it took until mid-January 2020 to get the product change approved in the customer process. It was originally thought that the cleaning would last six months, as the next boiler inspection was not scheduled until the beginning of July. Due to impending facility lock downs due to the COVID-19 pandemic, the plant outage and inspections where moved up to the end of April.
The pictures of the scale removal are from only three months of operation on the DReeM Polymer product. Scale removal has been significant on all the boiler waterside surfaces, and buckets of chip scale were removed from the mud drum.
Beyond just the visually obvious reduction in tube deposits, a review of natural gas fuel use for the two boilers for the months of January through May 2019 versus the same period in 2020 (the time the DReeM Polymer was started) show an average reduction of 8.6% and 19.4% respectively for boilers 1 and 2. As the boilers still have some deposition, the DReeM Polymer continues to clean the system and boiler efficiency gains have continued through 2020 since the boiler started back up.
DReeM Polymer™ Technology Cleans Boilers & Reduces Customer Fuel Spend
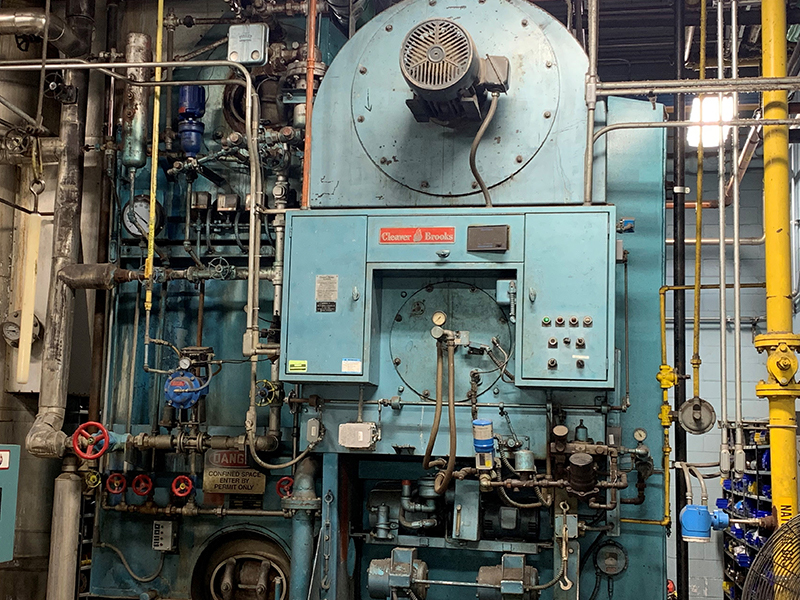