A large hospital has a campus wide seasonal chilled loop with approximately 75,000 gallons total volume. It was being treated using a traditional silica and azole-based corrosion inhibitor package. Corrosion coupon rates with the traditional inhibitor program were considered excellent for both mild steel and copper, yet each spring during startup, iron levels were found to be five to ten parts per million (ppm). This then required a flushing procedure of nearly half a million gallons of water over four days to remove these corrosion byproducts, which prevents fouling, equipment downtime, and poor heat transfer.
In order to minimize offseason corrosion, the hospital was previously circulating a layup chemical to passivate system metallurgy and minimize flash corrosion. Corrosion occurs due to the fast introduction of oxygen during the draining of the system each fall.
Another concern with the large campus loops are areas that did not get fully drained and dried out due to dead legs, poor pipe design, and/or low spots in piping. Over time, new construction and renovations to the facility’s systems increased the piping and volume, which lead to improper seasonal layup with their traditional chemical treatment. Humid and stagnant water locations increase general corrosion, and microbiological growth. These factors contribute to poor offseason corrosion protection and result in the high iron results found when testing the loop after initial startup in spring. Without initial flushing of the high iron levels, fouling can occur, resulting in poor heat transfer, increased energy costs and physical or chemical cleaning of heat exchangers and equipment.
With the customer’s challenges in mind, Kurita’s Cetamine was introduced to the hospital’s chilled loop system. The technology is a film-forming substance (FFS), which creates a hydrophobic barrier between the pipe surfaces and the bulk water. The treatment remains on the pipe surfaces after draining, allowing for protection against flash corrosion and during the offseason.
A residual of 0.5 ppm FFS was targeted on the loop during the first season using Cetamine, and iron testing during the season was routinely below one ppm. When discussing with the plant as to how to layup in the fall, Kurita and the facility decided to use Cetamine as opposed to the traditional layup procedure.
With about six weeks left in the season, additional chemical was added to boost FFS test results to one ppm for the remaining weeks. Immediately prior to shutdown, no traditional chemical layup (a $2,565 chemical cost annual savings) was added, which reduced the workload of facility personnel during a busy time transitioning between cooling and heating season.
After utilizing Cetamine in the chilled loop, corrosion coupon results came back excellent. The following spring, the system was filled and circulated. Initial testing of iron in the loop found it to have decreased from ten ppm to 0.54 ppm, a 92% reduction from previous year’s averages. This indicates a significant improvement in offline corrosion protection of the full system compared to the silica and traditional layup previously used. The low iron results indicated meant that the facility no longer needed to flush the loop during startup. Reduced iron also meant that offseason corrosion was significantly decreased, which extend building piping and equipment lifespans. Lower iron levels allow for improved heat transfer and reduced energy costs by preventing fouling and plugging of coils, heat exchangers, and other equipment.
Elimination of annual flushing resulted in water savings of 450,000 gallons, which is approximately three percent of the facility’s total cooling system water usage. Additionally, personnel hours were reduced by four days at a transition time between heating and cooling seasons. Annual costs for the Cetamine used in the loop were $1,660. With this information, the annual net savings for the customer was $5,865 per year, which equates to a return of 350% for every dollar spent with Kurita.
After reviewing the success of the chemical change in the chilled loop, Kurita and the facility are working to implement Cetamine throughout the facility’s other chilled and hot loops to better protect them both during operation and when offline.
Hospital Achieves Annual 350% Return with Kurita’s Cetamine® for Chilled Loop Systems
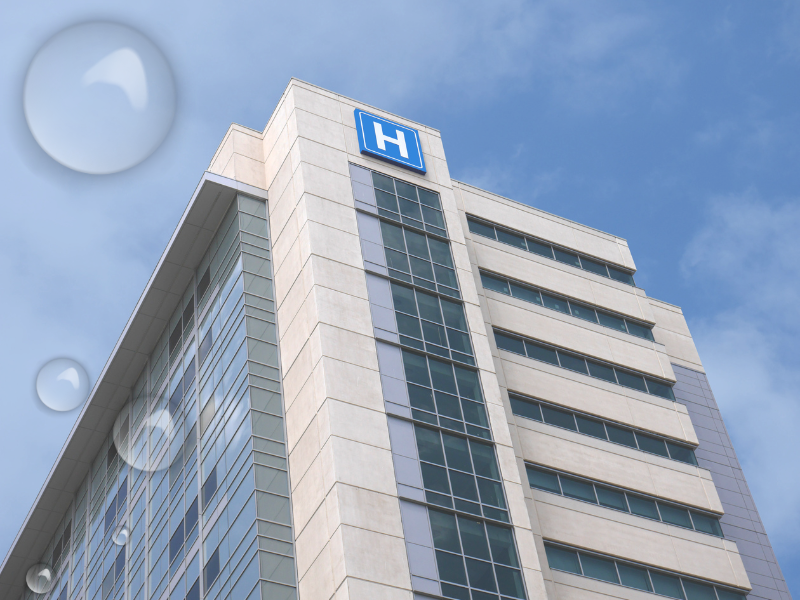