A Central Florida hospital was expanding their new central energy plant while phasing out an older steam plant. The hospital also has been experiencing significant condensate loss, and many of the heat exchangers were experiencing higher corrosion rates. The condensate loss also caused issues of controlling the pH level, which can corrode piping and equipment. This all accumulated into additional costs due to increased water, energy, and chemical usage, which increased operational costs. This hospital was determined to improve the water quality and minimize expenses associated with water, energy, and chemical usage.
The hospital decided to partner with Kurita because of their previous work in Florida and their capabilities in technologies, engineering, and services. In 2018, Kurita suggested using a reverse osmosis (RO) unit for the pre-existing energy plant to reduce chemical, energy, and water costs and to better treat the condensate. The hospital had reached its limited construction cost, so they were unable able to complete Kurita’s recommended RO unit.
As the new plant was being built, Kurita suggested EnergyOUT™ for the new construction, which would improve the water quality for the new steam plant. The hospital did not have any capital available for additional equipment, but the advantage of EnergyOUT is that there is no capital outlay by the customer. This provided an attractive return on investment (ROI) since it is a leasing system with service supplied by Kurita.
Kurita performed a complete system audit and worked with the customer to design the EnergyOUT system, including sizing for steam demand, while supplying engineering services on the backside. This incorporated a team of engineers and industry experts. Ultimately, the system needed to best fit the customer’s specific needs was identified.
Plants are often looking to increase their steam generation capabilities and boiler efficiency but do not have sufficient capital or budget for advanced pre-treatment systems. EnergyOUT is part of a Value+ program through an operating lease that includes equipment, standard service, and chemistries for a set monthly price. For the hospital – and all other applications – the cost spent on leasing the RO unit is made up by savings in water, energy, and chemistry. In addition to money saved on chemistry and fuel savings, EnergyOUT lowers a facility’s chemical, water and energy usage, and carbon footprint. The advantage of this application was the hospital used the RO reject water to supplement cooling water makeup to conserve water.
Once the EnergyOUT program was in place, there was an immediate reduction in chemical, energy, and water usage and improvement in condensate pH control. The condensate return line treatment program consumption was reduced by 80 percent. The hospital is saving over an estimated 291,000 pounds of CO2 emissions per year. The hospital not only has a 50 gallons per minute (gpm) RO system with no capital cost, but the lease cost is exceeded by the savings associated with the water, energy, and chemical reductions. The boiler cycles of concentration increased from 12 cycles to over 50 cycles, which resulted in a blowdown reduction of over 75 percent. The customer not only received savings to pay for the EnergyOUT program but an additional $30,000 in chemical savings as well as energy and water savings due to the lower blowdown rates. Additional results include increased heat exchanger life through better chemical control and overall lower utilities costs.
With this long-term partnership with Kurita, the hospital can expect regular maintenance from Kurita’s service team as well as daily monitoring of water quality. Currently, Kurita is also working with the hospital to increase cycles in the cooling towers with an acid trim chemical program and expanding the RO program for the boilers as the hospital expands. By continuing to partner with Kurita and employing the continuous improvement process, additional savings will be identified and implemented at the hospital.
Hospital Reduces 290,000 Pounds of CO2 Emissions Per Year with EnergyOUT™
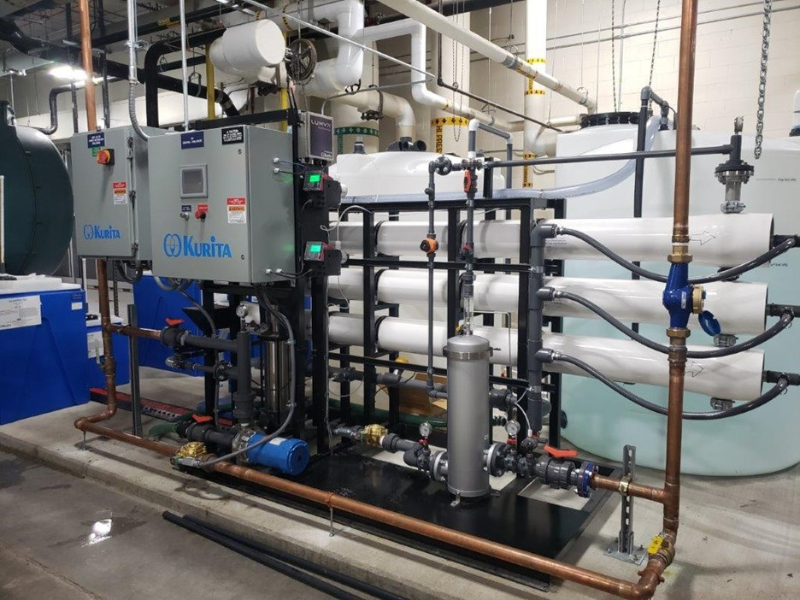