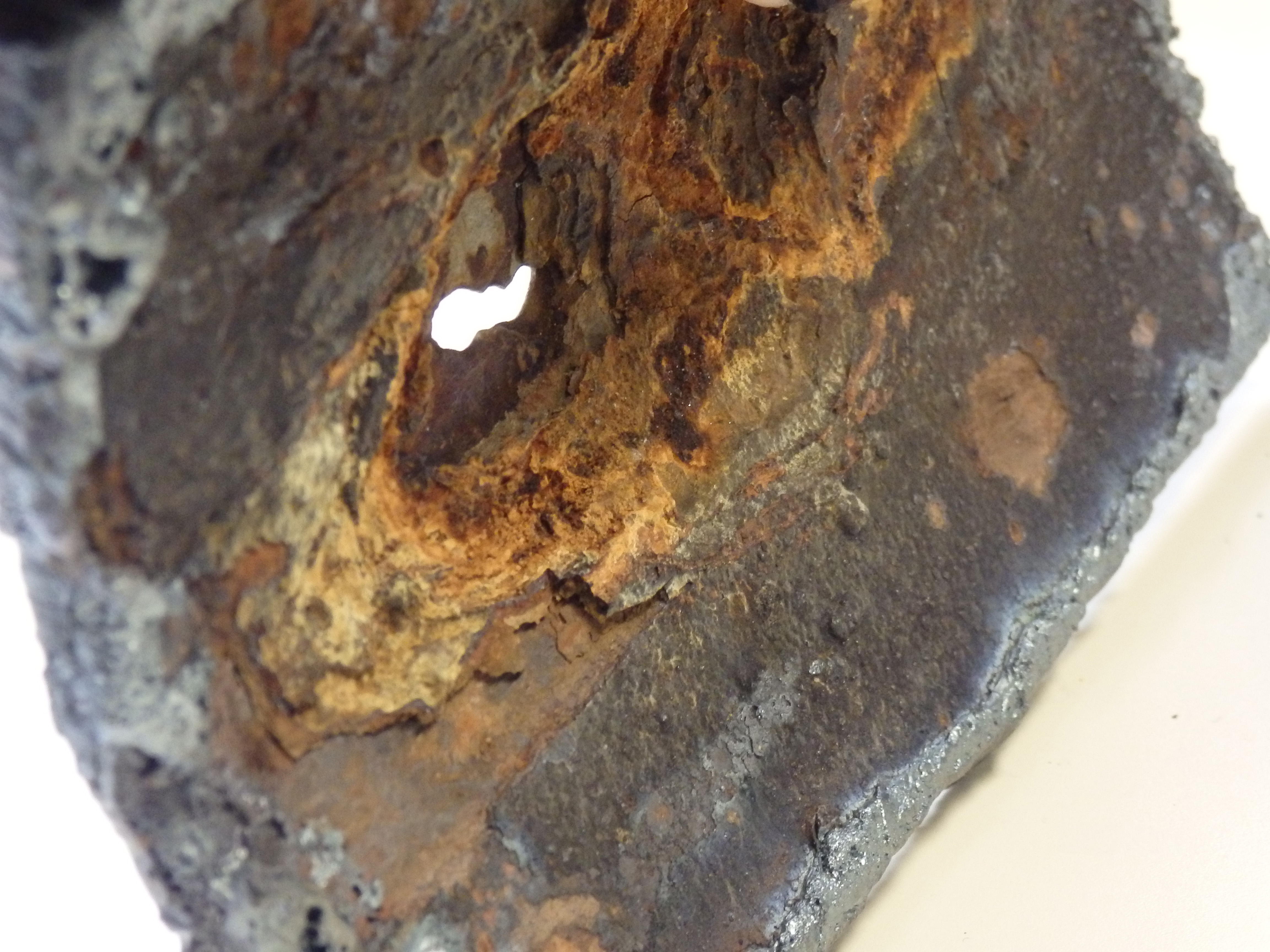
What is high purity water, and where is it used?
High purity water, also referred to as ultrapure or deionized water, must comply with quality requirements to sustain specific production goals and standards. It is used in a variety of industries where bacterial contamination is strictly regulated such as biopharmaceutical, electronics manufacturers, hospitals, laboratories and power generation (solar). Any testing results showing bacteria levels that are outside of acceptable limits may result in the loss of product and significant downtime.
Are there different types of high purity water?
Yes, specification levels are based on the requirements from governing bodies and include pharmaceutical, semi-conductor and reagent grade water systems. Product water such as Water for Injection (WFI), or an ingredient in drug product production carries United States Pharmaceopia (USP) designation. Water to be used in food is typically regulated by the FDA and must utilize “food-grade” equipment and instruments. Reagent water used for analytical purposes is subject to American Society for Testing and Materials (ASTM) standards. Once the system requirements and specifications have been defined, the treatment or piping system can be designed.
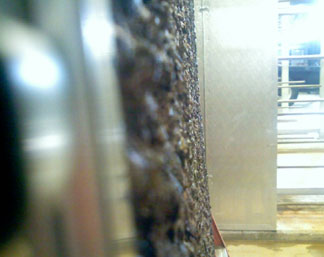
Water provides an ideal environment for bacteria to develop. Nutrients that bacteria feed off of can form on hard surfaces of water piping systems, and defects in piping, connection points, welds or fittings can contribute to bacterial contamination. The impact of bacteria growth can be detrimental to both the operational processes and performance requirement of the system product. For example, bacteria can greatly decrease the heat transfer capacity of heat exchangers, equipment commonly used to keep temperatures low in high purity systems.
Why is piping design important in high purity water systems?
Identifying and treating potential problems of bacteria formation once a system is in operation can be much more difficult than addressing them during the system design. Issues with bacterial growth on systems during operation are corrected by replacing or rerouting piping and heat tracing. During operation, if a leak or improper connection is located, manufacturers may choose to use heat tracing as a way to sanitize the connection and prevent the growth of bacteria or physical re-routing of piping. These corrective actions are not preferred as a final solution due to the ongoing expense associated with them.
What should be considered when designing system piping?
To prevent the growth of bacteria, the system engineer must consider nutrient sources, contamination sites, Colony Forming Zones (CFZ), piping materials and the location of corrective facilities when designing piping.
Nutrient sources are locations where the food can be introduced for different types of bacteria that are required for colonies to start and flourish. The most common source of nutrients in a system is from oxygen that occurs as part of the inherent piping layout or due to a mechanical operation such as a sample valve. CFZs are an area where, given the proper environment and nutrient availability, bacteria are allowed to grow and multiply. The most common CFZ that systems experience are “dead legs” or areas of low to no flow, greater than six diameters. Contamination sites are locations in the system, either in piping or system components, where nutrients enter the process loop. Minimizing or eliminating connections of fitting that allow air bleed within your piping layout is important. Certain piping materials, such as some plastic piping materials, can also allow oxygen to enter the system through absorption through the pipe wall. In this instance, the piping itself is a contamination site.
The installation of corrective facilities in piping systems allows for “access to the system for sanitization of introduction of steam, ozonation, chlorinators, storage at elevated temperatures,” etc.
How do you prevent contamination sites throughout the piping system?
Focusing on a piping layout that minimizes connections or fittings that allow air bleed is important, getting as near to a fully closed loop as possible. Fitting types are generally the limiting factor in mitigating the risk posed by contamination sites. The most common fitting type in a high purity system is the sanitary fitting (commonly called a tri clamp) connection, with threaded and even flanged connecting being seen as less proper. Threaded connections should not be used in any high purity application. Another tip during the initial stages of a system design is to focus on the connection types mounted on the physical components of a system and utilize tri clamp connections wherever possible. If tri clamp connections are not possible, butt fusion should be used to create a smooth and seamless connection.
How does the selection of piping material affect contamination?
While oxygen permeability of piping is not such a huge consideration when using stainless steel piping or tubing, it is an important aspect of dealing with poly piping. Typically high purity systems will incorporate the use of Low-Extractable Piping (LXT®), High Density Polyethylene Piping (HDPE), due to lower costs and ease of maintenance. The advantage of the LXT® piping is to prevent the leaching of extractable constituents such as chlorides and TOC from the piping into the process water. However, while both LXT® and HDPE offer some standard type fittings, the risk here comes from the fact that it is typically not possible to get tri clamp connections, which limits the sanitary design potential.
The best practice is to use high polished stainless steel for the process lines of the purity systems. As a part of quality control, all welds should be tested and examined. Bacteria can grow as a result of leaks due to improper welding or incorrect instrumentation connections, both of which may lead to the introduction of air into a system. It is also good practice to conduct regular cleanings or sanitations of any system with low bacteria level requirements.
What is the sanitization process once a system has been installed?
Water systems will contain bacteria, thus regular sanitization of the system is required to prevent the prolonged growth of bacteria. Sanitation should occur regularly, based on required testing and historical data. Sanitization requires that the system be taken out of service and flushed when complete, prior to returning to service. The most preferred and most common methods of sanitization include steam or ozonation. Some processes use heated permeate water instead of steam for heat sanitization.
In some instances, plants may choose to use sodium hypochlorite or bleach for sanitization. This method poses risks to the system. Overtime, bleach can be corrosive to stainless steel piping. Also, by using bleach, you are introducing a contaminant into the system. Lastly, many systems need to adhere to a chloride limit. These systems are required to monitor chlorine levels and may need to flush for a prolonged amount of time before being able return to service.
What are the common monitoring and sampling processes once a system has been installed?
Once a system is designed and installed, it is important to follow an approved monitoring and sampling plan to continuously monitor for bacteria levels. Point use of sampling, or sampling after the treatment component, is critical in identifying the locations of bacteria growth and contamination. The further upstream of a process that you can apply the performance qualification, the more likely you are to catch issues that may cause a system to fall away from expectations.
The method of testing can vary depending on the measured constituent and to what specification the system must adhere to. ASTM standards are available and outline the acceptable testing methods for water constituents and water treatment equipment. When monitoring, the use of proper instrumentation should be taken into account in order to give plants the ability to alert operations of significant changes from normal operating conditions. The limits of an alert should be defined and acceptable in accordance with the system requirements.