A successful water-management program for a process cooling water system will rely on a number of factors, some of which may be overlooked or ignored until a problem arises. There is much to consider in order to keep equipment operating efficiently, minimize rejection rates, prevent corrosion-related failures, conserve water and energy and reduce the risks associated with waterborne pathogens such as Legionella.
One mistake often made is to manage process cooling water systems in the same manner as an HVAC cooling water system. While it is common to see both types of systems within the same facility, they require different water-management programs. Process cooling water systems often have equipment with higher temperature heat transfer surfaces, greater operational complexity and higher levels of contamination than HVAC systems.
With this in mind, when developing a water-management program for a process water system, it is important to consider:
- Makeup or source water quality.
- Heat exchanger type.
- Process-side temperatures.
- Process and environmental contaminants.
- Whether a closed- or open-loop cooling water system will be (or is) used.
- System metallurgy.
- Operational characteristics.
- Regulatory limitations.
Process-Side Temperatures
Process-side temperatures influence the surface and water temperatures at the interface of the water and the equipment being cooled. This is true whether it is the tube wall in a shell-and-tube heat exchanger, or the surface in a plate-and-frame type exchanger or water-cooled mold or vessel. While cooling water temperatures may be in the range of 80 to 110°F (26 to 43°C), the temperature at the heat exchange/water interface may be considerably higher. In some cases such as in a steel mill continuous caster, it may be near the boiling point. This is important to consider because many scale-forming salts such as calcium carbonate are inversely soluble with temperature. Higher surface temperatures will also increase the rate of corrosion reactions.
Understanding how water temperature influences the water treatment program requires the input of those temperatures — along with the critical water chemistry parameters — into a basic scaling index calculation or with computer modeling. Two common scaling index calculators, the Langelier Saturation Index (LSI) and Ryznar Stability Index (RSI), work sufficiently well for establishing basic deposit control guidelines for calcium carbonate, but they are not applicable to other deposit-forming species such as calcium phosphate, calcium sulfate or magnesium silicate.
Once the properties of the heat transfer equipment have been established, the water chemistry needs to be reviewed to establish the initial limits on concentration ratio (cycles of concentration) based on the deposit-forming species. This will determine just one aspect of the overall water treatment program.
Table 1 below shows the impact of concentration ratio (cycles) on an example of makeup water at 100°F (38°C). Water treatment chemicals available to the market could responsibly treat approximately four cycles if well managed and other issues such as microbial fouling and proper flows are maintained. The temperature represented would be indicative of a low temperature process with refrigerant, an HVAC-type cooling system, or temperatures on the process side in the range of 100 to 120°F (38 to 49°C).
Figure 1 demonstrates how the scaling potential changes with increasing temperature using the example in table 1. This clearly shows the importance of understanding how and why higher temperature heat exchangers tend to form deposits more easily. It also shows why it is critical to base a treatment program on the estimated water temperature at the heat exchanger surface rather than the bulk water temperature or heat exchanger exit.
Keep in mind, it is not unusual to have multiple pieces of heat transfer equipment in a facility operating under different temperatures and conditions using a common cooling water source. In some cases, a treatment program may keep some surfaces clean while others may form deposits. For these reasons, a water treatment program always should be designed and controlled considering the highest surface temperatures.
In some instances, it may be necessary to reduce the concentration ratio (cycles) in a cooling water system. This will result in both higher water use and increased chemical use. An alternate option would be to reduce the pH and alkalinity of the cooling water using an acid such as sulfuric acid. By reducing pH and alkalinity, the solubility of many scale-forming species is increased, decreasing the tendency for deposits to form.
If a small percentage of the total cooling water used is for equipment operating with high surface temperatures, an engineering solution may be preferred. This may involve placing the equipment on its own dedicated cooling water system or installing an isolated closed-loop system with a heat exchanger to the existing cooling water system. Because closed-loop systems do not evaporate water, scale-forming minerals do not concentrate to levels that will form scale. In some cases, the existing makeup water quality may be all that is needed or, if required, reverse osmosis or demineralized water can be used. Systems such as those found in the continuous casting of metals or injection molding of plastics, where deposits on the water side of the mold can result in poor quality product and high rejection rates, benefit from or require a closed-loop cooling system.
Water Quality
The corrosive tendency of water also must be considered. Ions such as chloride (Cl-) and sulfate (SO4-2) are of primary concern. These ions interfere with passive oxide-film formation and will accelerate pitting-type corrosion. The indices (RSI/LSI) used for determining scaling tendency should not be used to indicate the corrosivity of water. These indices may help to determine the potential for calcium carbonate to form at the cathode of a corrosion cell, but they fail to consider corrosive ions and other factors associated with the corrosivity of water. One index sometimes used to provide insight into the pitting corrosion potential in domestic water systems is the Larson-Skold Index. Unfortunately, this index does not take into consideration temperature, pH, biofilm and other factors that may influence corrosion, and it is of minimal value in cooling water systems.
As a result, when considering the impact of chloride and sulfate concentration on corrosion, it is best to rely on empirical evidence based on similar quality water used in systems with comparable operating conditions. This type of information can be provided by an experienced water treatment professional.
System Metallurgy
Another important consideration is system metallurgy. Cooling water systems will contain mixed metallurgies that might include stainless steels, copper and aluminum alloys, and carbon steel. Some may contain highly specialized materials such as Nickel Alloy 20 used for processing certain acids or other highly corrosive environments.
Alloy selection should be based on both water quality and process-side requirements, but such selections often are made solely on process-side requirements — with little regard to cooling water quality. For example, a 254 SMO stainless steel heat exchanger would be a better choice than 304 or 316 when the cooling water chloride levels would present a risk for crevice corrosion — even though 304 or 316 would be a suitable alloy for the process side.
Avoiding designing in or creating galvanic corrosion also is a concern. For instance, do not use copper tubing and brass fittings plumbed directly to an aluminum injection mold or install a brass heat exchanger with carbon steel baffles. Cooling system metallurgy has been of increasing concern with the emphasis on water reuse. Cooling water systems have become the sink for a number of reclaim source waters that may not be of suitable quality for the existing metallurgy. Reuse waters often are very high in corrosive ions, phosphates, suspended solids, ammonia nitrogen and organic carbon, which serves as a nutrient for microbial growth.
Galvanized cooling towers often are used for small process cooling water applications even though these types of coatings are subject to white rust when cooling water pH exceeds 8.3. A better choice for alkaline cooling water systems would be stainless steel, plastics or nonmetallic coated towers.
Microbiological Control
Cooling water microbiological issues often are mistakenly overlooked as secondary to scale and corrosion. Uncontrolled microbiological growth and excessive biofilm formation will lead to a multitude of issues, with fouling of heat exchangers, equipment and cooling towers being the most obvious. Biofilm on surfaces also can be influential in the formation of inorganic deposits through microbial mineralization.
Microbiological corrosion (MIC) is a significant and common problem. MIC often is associated with sulfate-reducing bacteria (SRB) and iron-oxidizing bacteria, but there are a number of mechanisms by which microorganisms cause corrosion. These include the production of organic acids, ammonia or simply by the microorganisms being present on the surface and interfering with passive-film formation or repair.
One of the parameters that should be tested when looking at the tendency for a cooling water system to have biofilm-related issues is total organic carbon (TOC). Organic carbon serves as nutrient for microbial growth, and the higher the organic carbon, the more available nutrient for microbial growth. HVAC cooling towers may have TOC levels ranging from 20 to 50 ppm while process cooling water systems can have levels in the 100s of ppm.
Testing and trending of organic carbon does not require expensive instrumentation. While expensive TOC analyzers may be the best way to measure TOC, a simple test for use with handheld or bench spectrophotometers is available. While not all organic carbon is biodegradable, this does hold true as a general rule.
Compared to HVAC cooling water systems, many process cooling water systems may be subject to continuous or intermittent contamination, which can make microbiological control challenging. Unintended contamination from a process leak may result in a rapid increase in biofilm, quickly fouling heat exchangers or cooling tower fill — sometimes overnight.
A small process leak in a heat exchanger may go unnoticed, but it can add enough organic nutrient to increase microbial growth and cause fouling. Direct-contact cooling water such as roll cooling in a steel mill or plastic extrusion processes will be contaminated continuously with oils or other products used in the process. Another example is breakage of containers in canning or bottling, where such breakage will contribute significant nutrient. Cooling towers also act as large air scrubbers removing particulate matter, gases or volatile vapors from the air. These contaminants will add to the nutrient loading in the cooling water and increase fouling potential.
In addition, manufacturing environments may have local conditions that attribute to a high level of airborne contaminants. For example, food plants may have exhaust from cooking processes present, and fuel ethanol or distilling may have contamination caused by grain dust. These contaminants not only increase microbiological activity but also place significant demand on oxidants such as chlorine or bromine used for biofilm control. Alternative oxidants such as chlorine dioxide often are used because they may not react with process contaminants as readily. In addition to greater oxidant demand when compared to HVAC systems, process systems may require a higher dose and frequency of additional non-oxidizing microbicides to maintain control.
Another key to the success of a cooling water-management program is total suspended solids (TSS). Suspended solids in cooling water may be due to airborne particulates, precipitation of insoluble salts or corrosion byproducts, process contaminants or microbiological growth. Cooling water high in suspended solids will have a greater tendency to foul, especially in low flow areas, plate-and-frame or shell-and-tube heat exchangers, cooling tower fill or in equipment with small orifices. Biofilm will act to trap these suspended solids, creating significant fouling issues.
Most cooling water systems will benefit from side-stream filtration to remove suspended solids. Such filtration systems can be part of an integrated approach to cooling water management. Before installing a filtration system, the water should be tested to determine which micron size filter will be effective. A particle-size analysis will determine the size distribution for the water to be treated. If the majority of the particles contributing to TSS are under the size rating for the filter, it will not be effective in minimizing fouling. A number of filtration options are available for open and closed cooling water systems. Self-backwashing multimedia filters are a good choice for open cooling water systems while replaceable cartridge or a sock-type filters may be adequate for most closed systems.
The final consideration is defining how each component of the cooling water system is operated. Systems or heat exchangers with constant flow respond best to treatment because they are continually being exposed to deposit, corrosion and biofilm control chemicals. Those operating with periods of downtime, however, often are plagued with issues, especially with corrosion and MIC. When a system shuts down, suspended solids in the water will settle out, contributing to fouling and localized corrosion. Scale inhibitors and dispersants will adsorb to levels below the amount required to keep deposit-forming species dispersed or in solution, and deposits may form. Oxidizing microbicides rapidly deplete and, if a non-oxidizing microbicide is not present, fouling or MIC may initiate.
Once such problems are identified, operational changes can be made to minimize issues. Depending on the nature of the equipment and metallurgy, recommendations may include adding an automated full-flow flush cycle to remove precipitated solids and expose the surfaces to microbicide and corrosion inhibitor. Simply draining and drying the equipment may be appropriate for some systems. For systems down for extended periods, a layup program is the best choice.
Taking into consideration the points raised in this article will provide those involved in water management with the foundation of knowledge needed to develop, implement and maintain a successful program.
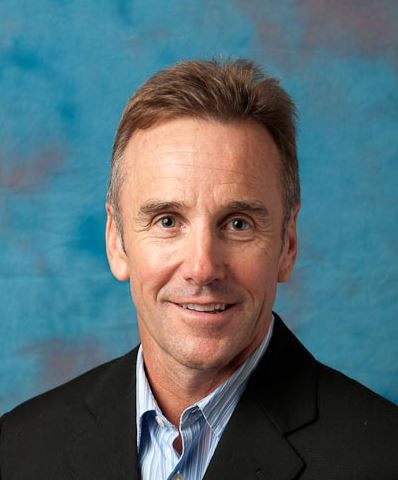
Jim Lukanich is the Director of Applied Technologies for Kurita America. Jim’s career in the water treatment industry began in 1981 and since then he has served in a number of roles including, field sales, technical support, training, research and development and as a technical consultant.
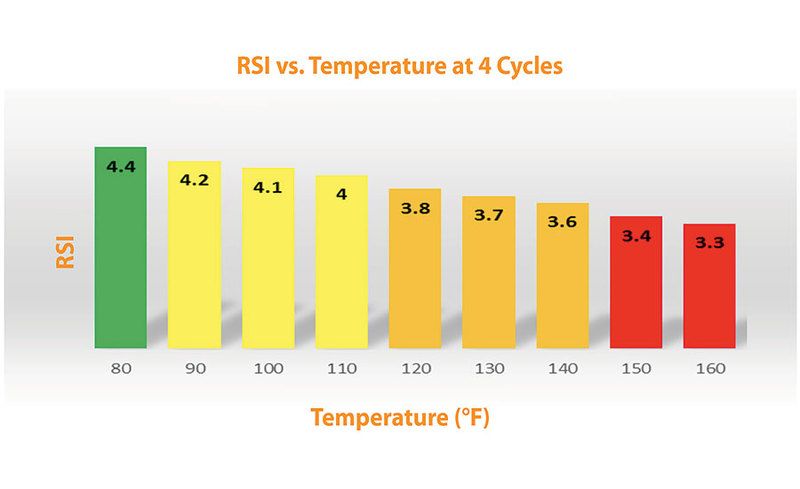
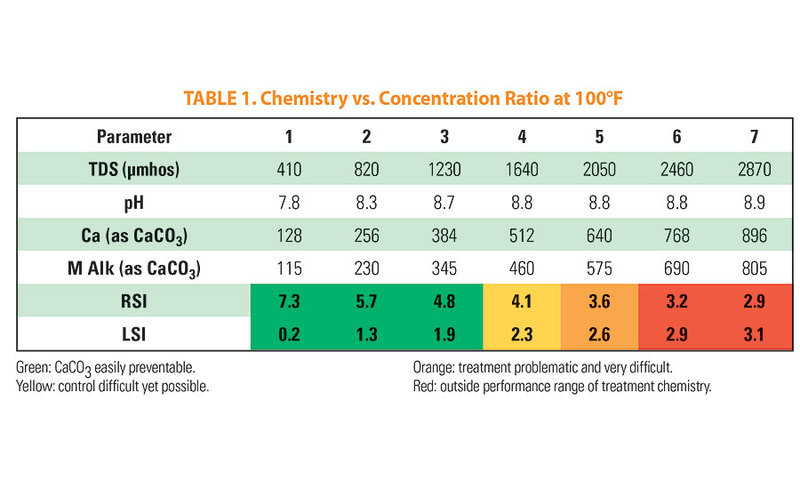
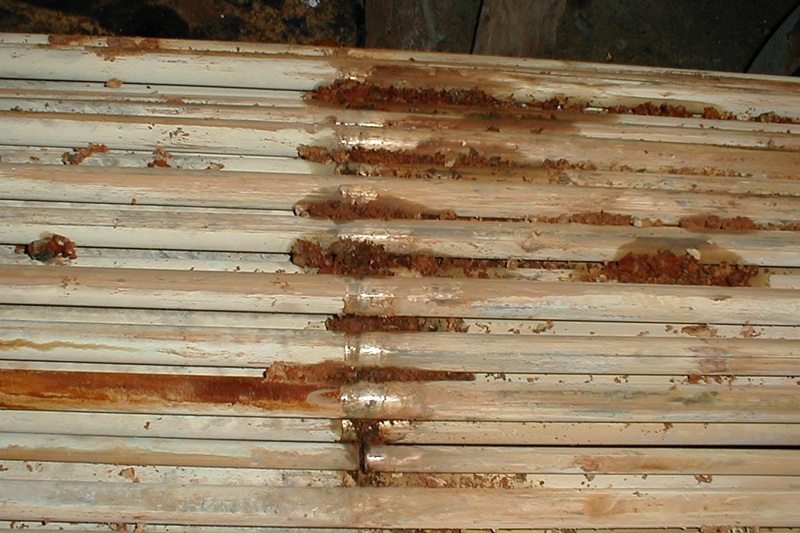
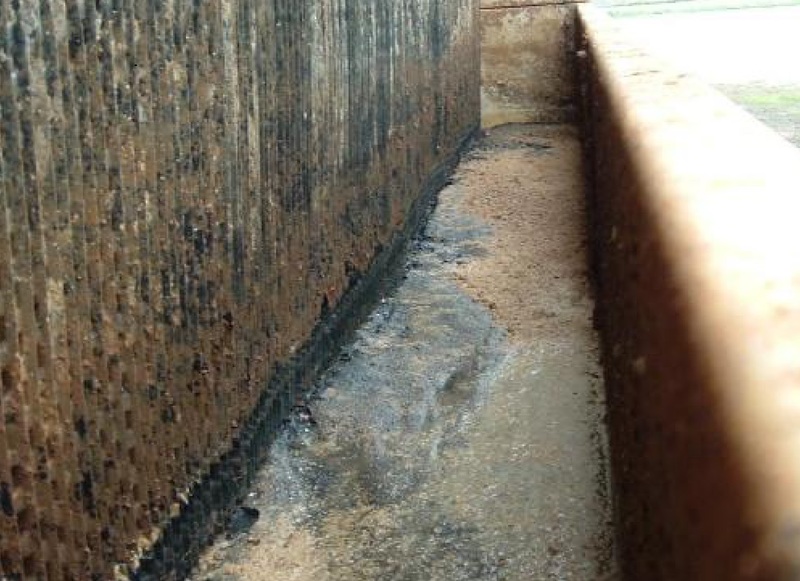