In compliance with their existing water discharge permit, Saint John’s University’s central plant discharged their boiler streams to an on-campus wastewater treatment plant with the cooling tower blowdown discharged to a nearby lake. However, when the plant underwent the renewal of their water discharge permit, they faced new, tighter discharge limits.
The new permit limitations required significant reduction in the amount of phosphorus discharged to the lake. Like most facilities, Saint John’s University, located in Collegeville, MN, was using a traditional phosphorous based program for corrosion and scale protection. As receiving water streams become more susceptible to algae and aquatic plant growth, phosphorus discharge limits have been scrutinized and, in some counties, drastically lowered to control this issue.
The campus wastewater treatment plant did not have sufficient capacity to accept the cooling tower’s blowdown. After several months, the current water treatment supplier had no success in developing a cooling chemistry program which met the new environmental discharge restrictions. For this reason, the university staff reached out to other companies for assistance, contacting Kurita America in the process.
Kurita America proposed the use of its unique PhosZero™ Technology which contains no phosphorus while still providing excellent corrosion and scale protection equivalent to, or better than, traditional cooling water treatment chemistry.
The new permit limitations also affected the use of oxidizing biocides. Since the blowdown was being directed to a lake, there was concern that any biocide residual would affect aquatic life in the lake. Chloride discharge was also a concern, which restricted the use of sodium hypochlorite or other chlorine-based biocides. Kurita America proposed the use of a biocide that blended hydrogen peroxide and peroxyacetic acid.
A program was designed to control biocide feed in a way that provided excellent microbiological control. Importantly for the discharge concerns, this blended biocide degrades quickly reducing the environmental impact. To further ensure compliance, prior to the final discharge, a small amount of sodium bisulfite is added to the cooling tower blowdown to complete the neutralization of the biocide. As a final step in the new water treatment program, a Kurita America automation and control system were installed to provide real time information on the operation of the cooling towers, which provided the benefit of minimizing cooling tower makeup and chemical costs.
Kurita America’s Engineering team met with the state regulatory agency and presented the necessary toxicity data and detailed operational plan to obtain agency approval. Permit approval for the proposed program was finalized within 3 weeks. The program was implemented in late 2013 and results of sampling during 2014 confirmed compliance with the state permit while providing improved scale and corrosion control when compared to the traditional treatment approach that had been used previously.
Saint John’s University Operations Meets New Water Discharge Permit Limitations
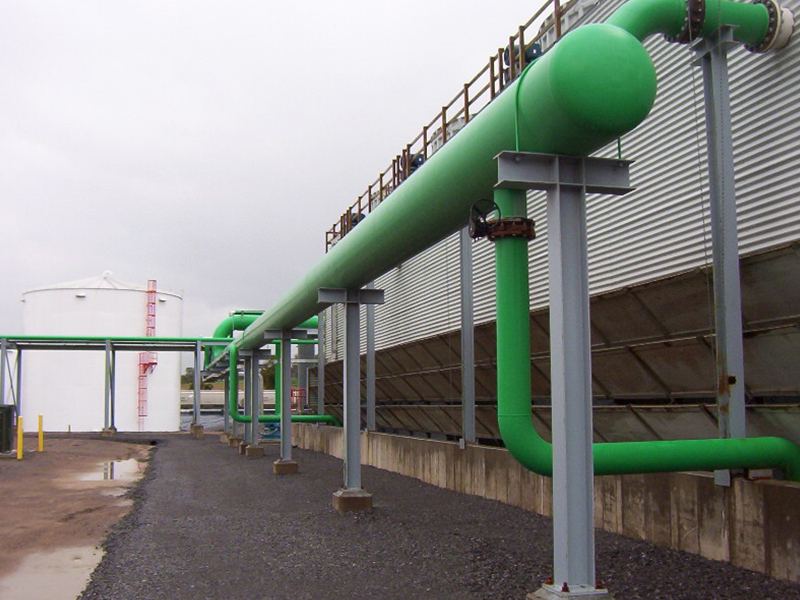