Published September 2021, revised July 2024
Dirty and fouled cooling tower water often plagues maintenance teams that manage industrial cooling tower operation. A dirty cooling tower can have a detrimental effect on the overall health of the plant’s water infrastructure, leading to lower efficiencies and increased costs. Cooling water full of fine sand, grit, and biological matter can contribute to damage to analytical instrumentation, creating inaccuracies and premature failure. High solids can give rise to increased deposition of debris within a cooling tower basin, which can provide a home for corrosive anaerobic bacteria.
With increased debris and organic matter, manually cleaning a cooling tower can take days to accomplish. All these factors contribute to unnecessary downtime, failure of instrumentation, decreased efficiencies, and increased water and chemical usage.
Bag or Cartridge Filtration Technologies
As some of the lowest-cost offerings in cooling tower filtration, bag, or cartridge filters are readily available. Typically, pending the design requirement, they cost less than alternative solutions. Many options exist for the types of filter media and materials of construction.For a bag or cartridge housing to be effective, a few factors should be considered. First, the housing needs to be sized based on system flow rate and the desired level of filtration. Second, to utilize the full dirt-loading capabilities of the filtration technology selected, the preferred installation location typically is a place where a high differential pressure is available. This can be accomplished by installing the filter near the main system recirculation pumps and sending the filtered water to the tower basin or sump. If decreased cooling water capacity is a concern, another option is installing a circulating pump to provide the necessary flow and pressure.
One benefit of selecting a bag or cartridge filter is the ability to change the retention rating on the filter whenever desired. Bag filters typically are used in higher flow applications or where larger particulate is prevalent within the system. Cartridge filtration is preferred in conditions where lower flows may exist; typical uses include applications where lower micron ratings are needed for particulate removal, or where the ability to extend the filter life between change-outs is important. Bag and cartridge filters are offered in several materials of construction and sizes.
The notable costs associated with bag and cartridge filtration are the initial costs of the housing and the recurring cost of replacing the filters.
This article offers a brief overview of several common solutions that exist for tower water filtration. The highlighted benefits may be helpful in deciding which type of filtration to choose for your cooling tower.
Sand Filtration
The second common offering that can be used for side-stream filtration on a cooling tower is a sand filter.Typically, a sand filter is constructed of a large fiberglass or stainless vessel that filters out particulate. Within the filter, the water passes through a layered sand-and-gravel mixture. The flow of water through the sand filter typically is top-down. As the particulate begins to collect on the top layers of sand, the differential pressure rises. Once the differential pressure reaches the designed level, a backwash process is started. The backwash process uses either system water or an external source (like city water) to rinse and remove the collected particulate from the sand filter, and this rinse water is sent to waste.
Sand filters are sized based on flow rate. Most sand filters can remove down to five microns on average, though 20 to 30 microns is typical. High efficiency sand filters on the market can remove even smaller particulate matter if necessary.
The initial capital cost on this type of filtration equipment is higher than bag or cartridge filters. Operational costs with sand filters are low, however. They include media replacement and the cost of water needed to backwash. Further treatment of the backwash wastewater is uncommon, but it must be evaluated. Sand filters can be extremely beneficial for an application where there may be high solids loading, and at plants with limited maintenance personnel.
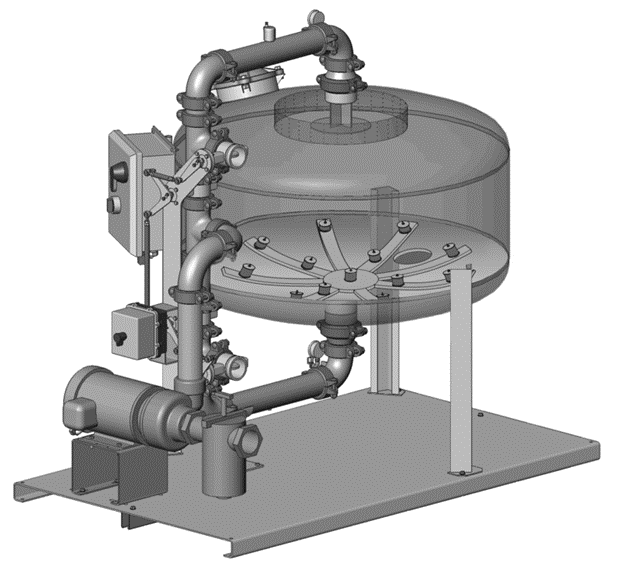
Drawing of a typical sand filter set up. Process water enters the filtration via the pump inlet strainer, exits the volute of the pump, enters the top of the tank and filtrates through the sand and gravel mixture before exiting out the bottom of the tank and returning to the process. (Image Courtesy of Lakos; www.lakos.com)
Centrifugal Separators
Centrifugal separators usually are not sized for very fine, low density particle removal due to the time required for the particles to be removed. The simplistic nature of this type of side-stream filtration with minimal waste is often attractive. However, drawbacks and capital costs should be considered.
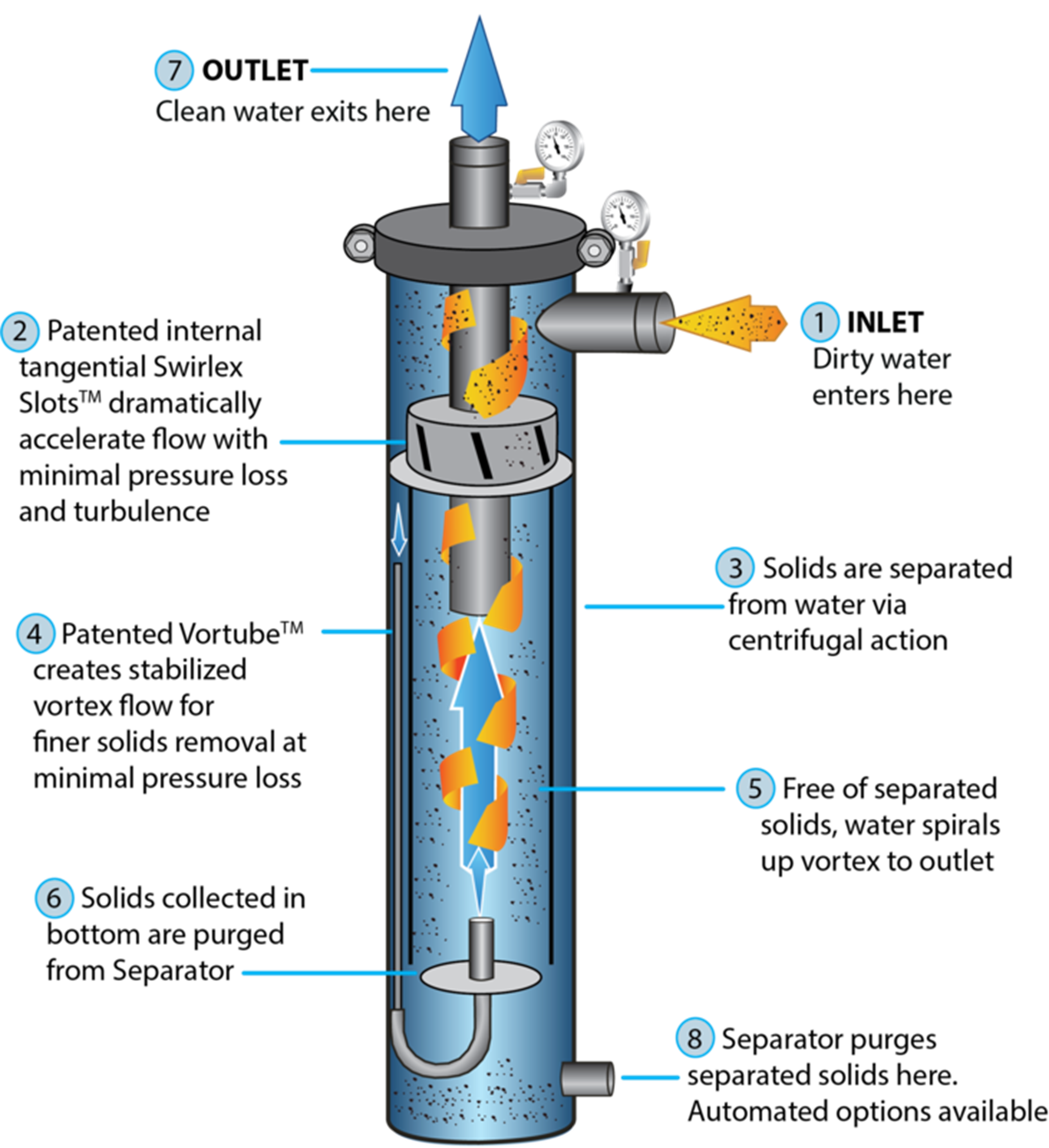
Self-Cleaning Strainers
A strainer consists of a housing and controls that regulate flow across a metal basket or screen that can trap particulates. After a timed delay or a differential pressure across the strainer is reached, water flow is reversed and sent to the drain to flush the collected solids.
A self-cleaning strainer can assist in catching particulates and treat higher flow rates at a reduced cost compared to other options discussed. There is no replacement media with self-cleaning strainers, but they carry a higher capital cost than comparable offerings. The operational costs are limited to only water usage and electricity.
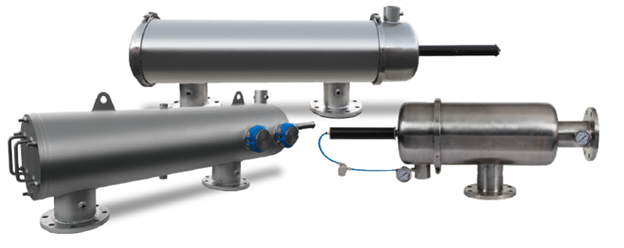
Self-Cleaning Strainers are used to capture larger particulate to automatically send to waste. Shown above are a few examples of what strainers look like. (Image Courtesy of Lakos; www.lakos.com)
Accessories to Augment Filtration Technologies
When thinking about cooling tower filtration, it is important to remember that the filter is only capable of removing particulates suspended within the water column. Optimally, an ample amount of agitation should occur inside the cooling tower basin to prevent debris and particulates from settling and accumulating tower basin floor. In many installations, it is recommended to consider a sweeper package system to agitate the basin.
Typically, a sweeper basin package is operated using a high-pressure pump that can propel water through the filtration system and then through a series of nozzles within the tower basin to keep the settled debris agitated and suspended. A properly designed sweeper basin package or plan to agitate the water can have strong positive effects on the life of the cooling tower. Allowing dirt and debris to settle on the horizontals sections in a cooling tower can promote biofilm development and the potential for corrosion under the deposits.
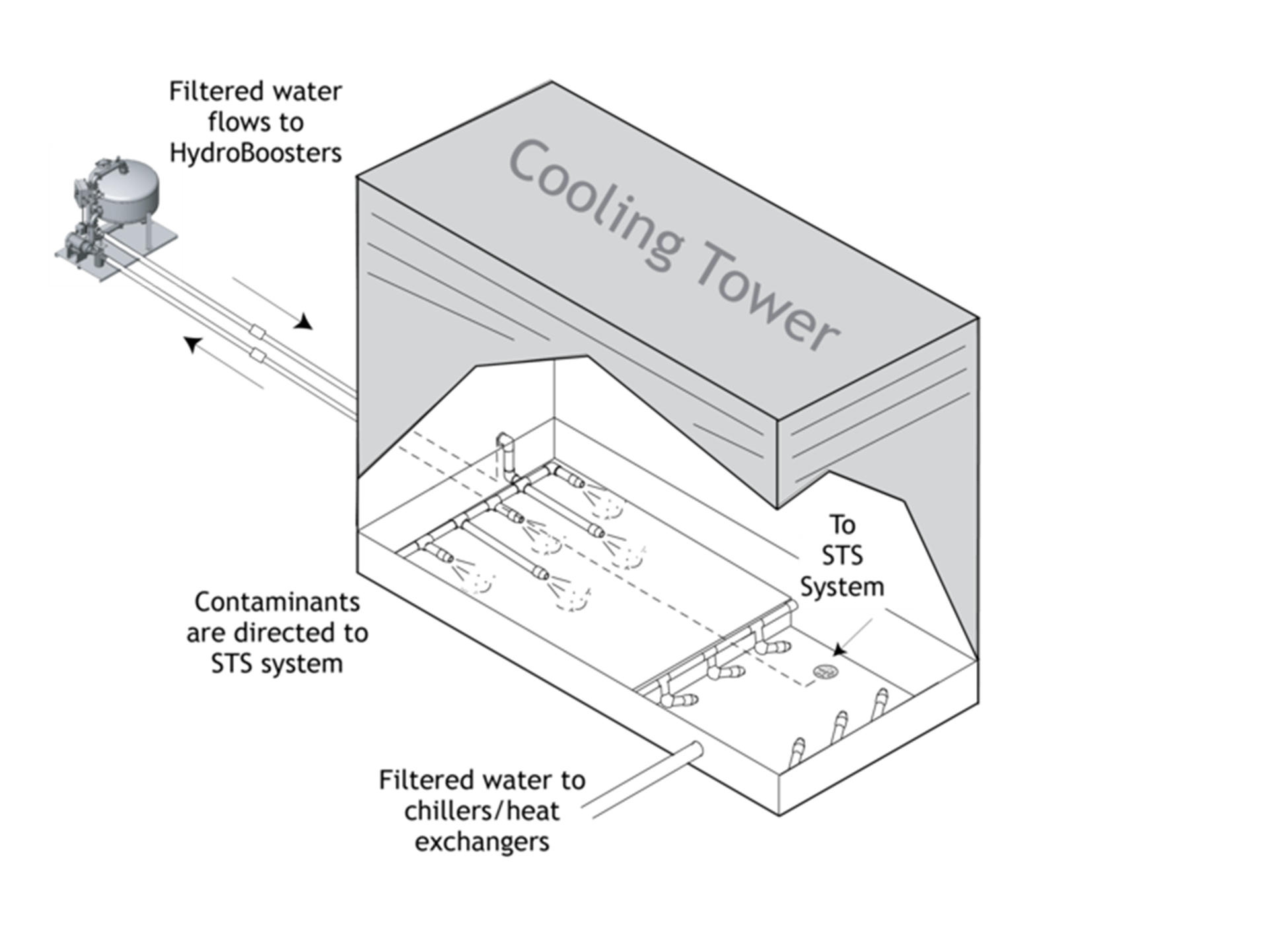
Sweeper Basin Packages offer the ability to keep cooling tower basins cleaner longer. In the example above: a sand filter is used as the primary source of filtration providing the flow of water through the basin. The basin sweeper package typically involves pipework and nozzles designed to produce pressurized flow to centralize and keep particulate suspended in the water column making it easier to remove. (Image Courtesy of Lakos; www.lakos.com)
In conclusion, with the internal and external pressures higher than ever to reduce operating costs, companies and maintenance teams need to seriously consider investing in cooling tower filtration. The benefits of operating a clean cooling tower are immense.