Maximized Production
Kurita America's pHytOUT® technology increases operation runtime by 600%
Improved Quality
Better economical performance of your DDGS with reduced S-content
Energy Savings
pHytOUT® Technology and ProHib product range allow better heat transfer and decreases the use of Acid
Process Flow and Solutions
Together, we can achieve your facility’s goals.
Click through the diagram below and see how Kurita America’s Total Solutions water and process capabilities can help you increase overall plant profitability.
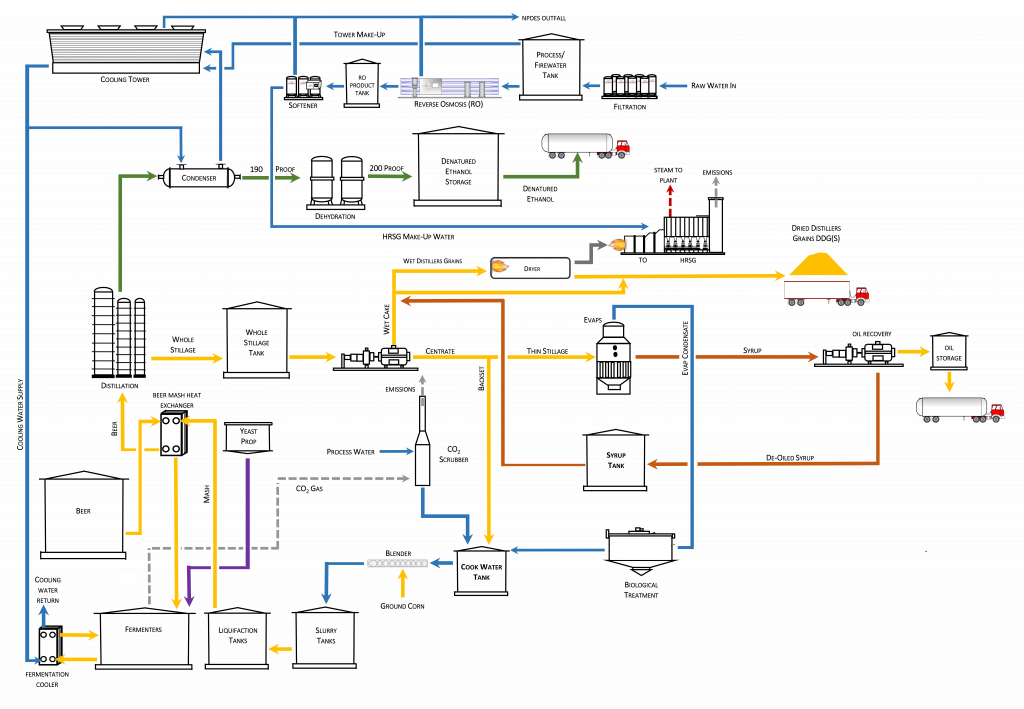